Quality Management
Quality Baked Right In
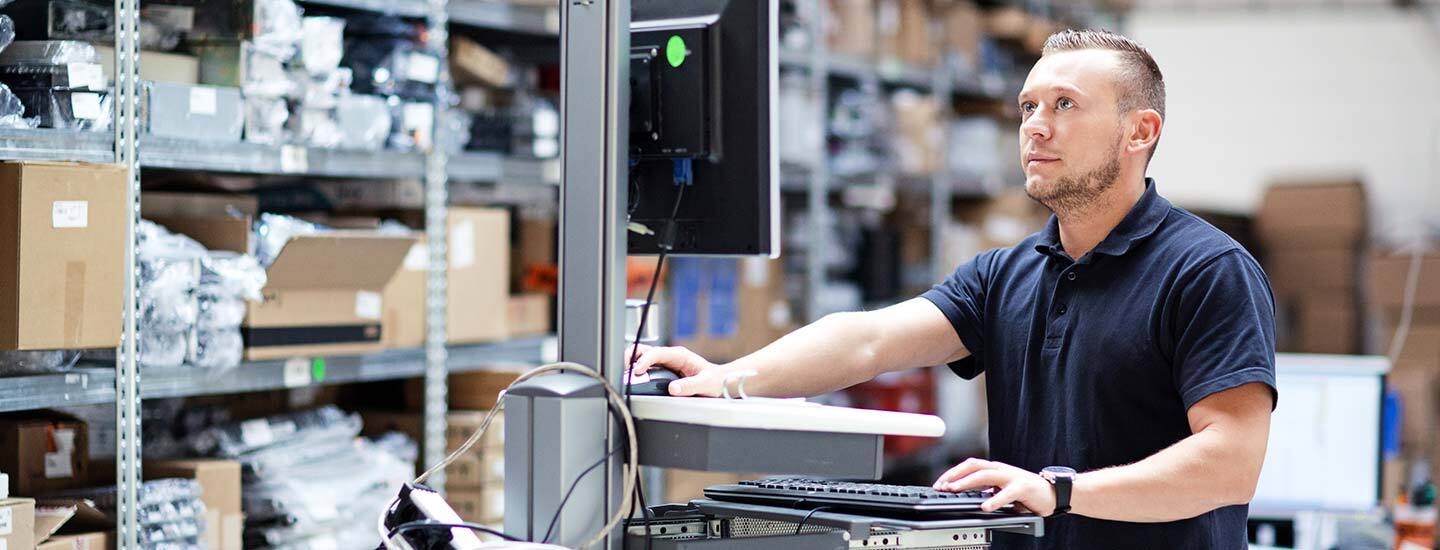
Customers expect products manufactured to specification and delivered on time. Quality is assumed. With so much competition for every job coupled with slim margins, no manufacturer can afford to spend time and money on rework. A quality system fully integrated into your operations allows your company to easily collect and analyse data to identify production problems earlier in the production process, thereby reducing rework, returns, and customer complaints.
Today, many companies require or prefer their suppliers to be ISO 9001 certified. Anyone who has been through the process knows that the time required to pass an audit and achieve certification is significant. One of the most time-consuming aspects of certification is documenting your business processes. Your system forms the framework within which your business operates and is an integral part of your ISO 9001 certification process. Pre-defined templates of each business process go a long way in helping you create the necessary documentation required for certification.
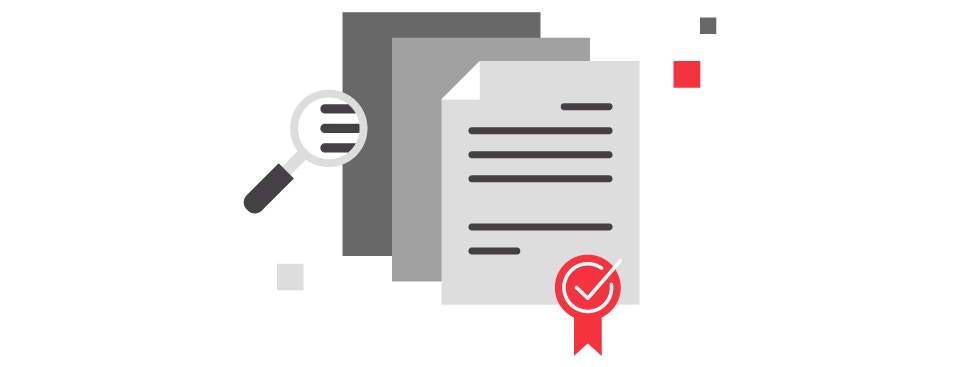
Key Questions:
- Is the quality module part of the core system or a third-party addition?
- Does the system automatically collect all quality data?
- Does the system schedule and track all preventative maintenance?
- Does the system help you identify and control potential problems before they affect due dates or quality ratings?
Ready to Transform Your Job Shop?
Take the first step towards operational efficiency and business growth. Fill out this form to get in touch with our ERP experts who can guide you through the selection and implementation process of our ERP software for job shops, machine shops, and make-to-order manufacturers.