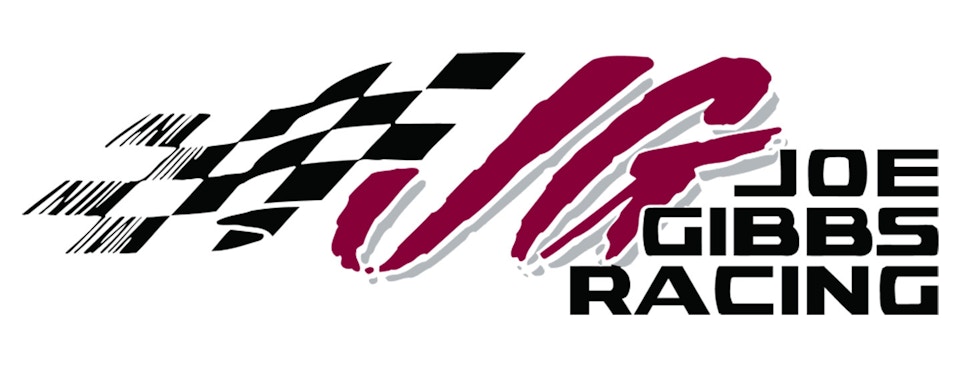
About Joe Gibbs Racing
What began as a dream came to life in Huntersville, NC, in 1992. Joe Gibbs Racing has become a premier NASCAR race team, winning five Cup Series Championships and four NASCAR Xfinity Series Championships. In addition to supplying its internal team, Joe Gibbs Racing also extends its high-quality products to external customers, including the Navy, Coast Guard, and aerospace industries.
The Challenge
When Joe Gibbs Racing began, its only customer was itself. There was no need for vigorous quality management, organized data documentation, or regulatory compliance since the only customer they needed to appease was themselves. This all changed when the shop decided to use its manufacturing capabilities to provide parts for the outside world. Steven Lee, Quality Manager at Joe Gibbs Racing, explains that with the decision to expand, the shop would now need a powerful system that could handle all the demands of external customers.
“We needed to really build a good quality management system that wasn’t initially necessary when we were our own customer,” Steven explains. In 2009, Joe Gibbs Racing adopted JobBOSS to control the manufacturing jobs running through the shop while they made components for the race cars. uniPoint was then added to the shop's technology about three years ago.
“It’s been about three years now that we’ve really built a quality management system, and uniPoint has been key to being able to implement it.”
The Solution
Upon implementing new technology, Steven remarked that it took the older employees a minute to catch on, but that implementation was fairly easy and quick. He also noted, “We were able to build out the system without having to hire at least two extra people that it would have taken if we were gonna do it on paper. The biggest difference is the availability of the data when we’re capturing it as we go now, and it’s pretty easy to pull it out and report it.” This helped the manufacturing portion of the company profit successfully.
Quality documentation is vital when working with aerospace and government clients. As Steven explained, “With aerospace customers, you have to have the paperwork right before they even look at your parts.” uniPoint has helped Joe Gibbs Racing in this area by automating AS9100 forms, saving the company time.
“We take our data that's already collected during the process, and it fills the forms and gets it ready to go for them quickly. So, that'll just be a lot quicker to submit, finish the paperwork, and be ready to ship sooner because now, we don't get paid until a part ships. You know? If they're sitting on our dock, we're not getting paid.”
The data uniPoint collects not only helps with compliance, but with all processes on the shop floor. Inspections and preventive maintenance on equipment is more streamlined with real-time data collection. Rather than waiting on travelers or word-of-mouth, uniPoint helps Joe Gibbs Racing track nonconformances and see trends with data to coincide.
When it comes to compliance, data, and quality, Joe Gibbs Racing trusts JobBOSS and uniPoint as the solution that encompasses it all. We cannot wait to continue working with them and watching as the shop grows and continues to find success in all it’s endeavors.
Watch the Webinar-on-Demand to learn more about how Joe Gibbs Racing uses uniPoint
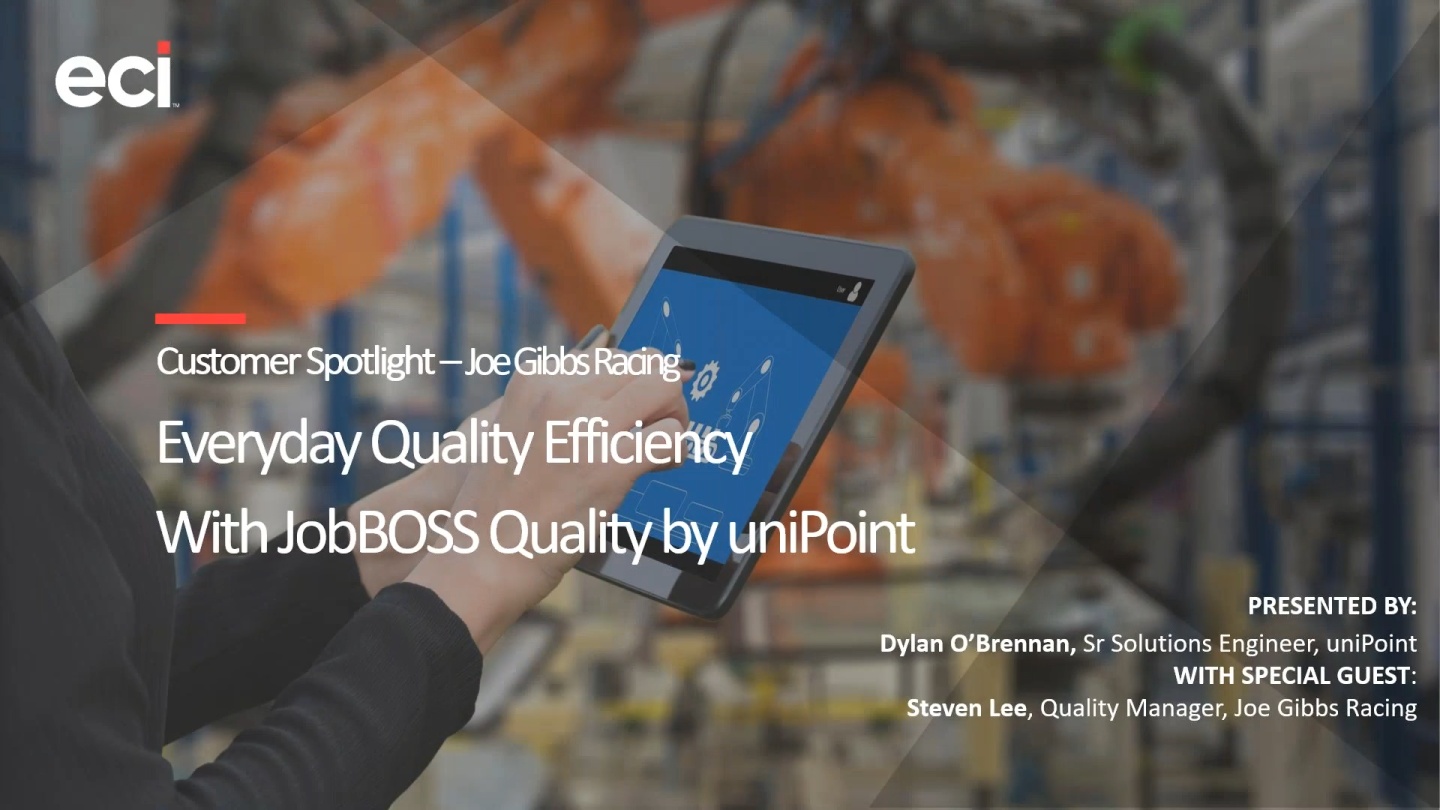