ERP Buyer's Guide Part 3
How to Determine ERP Functionality Needs
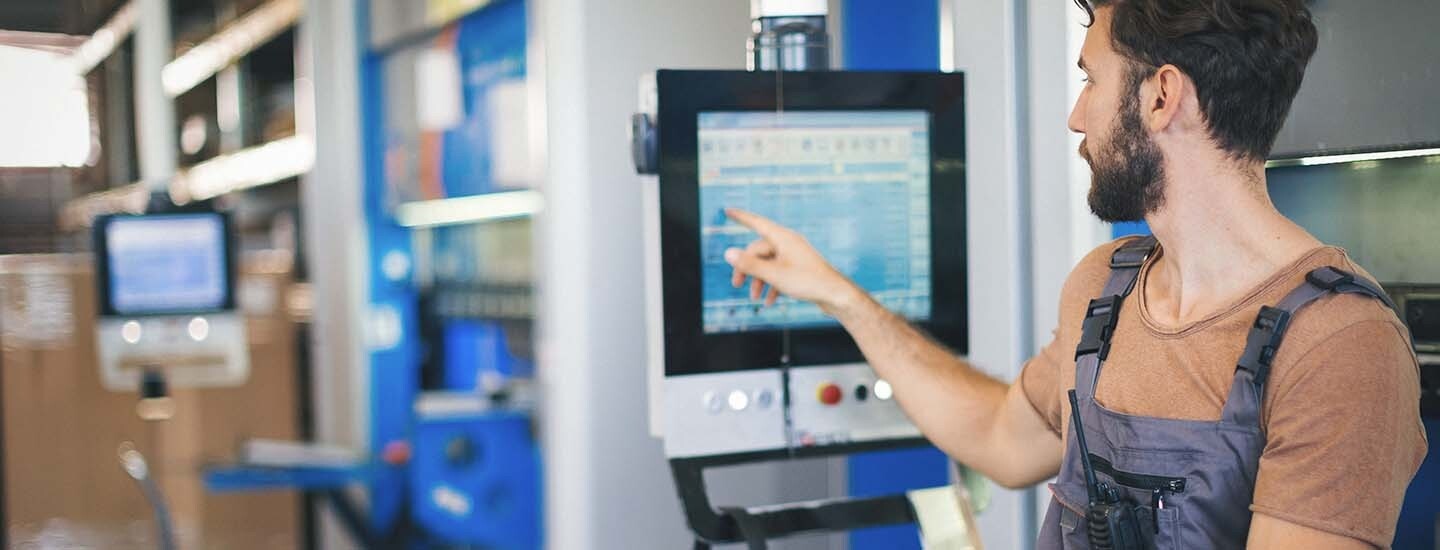
Maximizing your business potential
To compete in this environment, a 21st century Enterprise Resource Planning (ERP) solution is a necessity, especially for smaller and medium-sized businesses (SMBs). Today’s manufacturing-specific solutions structure and align your business processes for optimal efficiency and productivity. Choosing the right ERP for your operation will maximize business potential in every area from purchasing and sourcing to manufacturing and inventory processes, to sales, marketing, distribution, and customer relationship management.
In this report, we provide a guide for understanding your ERP functionality options and determining your business’ unique needs. In a crowded ERP solution marketplace cluttered with confusing advertising messages, it takes a methodical approach to match the right solution to your business. This involves clearly defining your purpose, assessing your business requirements, and having qualitative and quantitative objectives. It requires an understanding of the baseline technologies you will need to make your investment worthwhile, the common functional components every manufacturing ERP solution should include, and the specialty functions and software module integrations to consider.
To clear the deck of solutions that should not be considered, we begin with the functional requirements for every manufacturing and job shop SMB.
Core ERP functional requirements
For manufacturing and job shop SMBs, there are several functionalities and features that are business imperatives, and will only increase in importance as technology advances and the economy fluctuates. We suggest eliminating any systems from contention that do not meet these functional requirements.
A 21st century technology platform
Unfortunately, the manufacturing industry is riddled with outdated, outmoded 20th century technology platforms that stifle the growth capabilities of businesses that invest in them. These systems use layers of cosmetic add-ons to appear up to date but if you investigate carefully, many lack end-to-end integration as well as much of the functionality described in this guide.
21st century systems are wholly integrated, seamless solutions that enable all functional areas of your business to work from the same continually updated data. Your ERP solution must do this in order to be a centralized business management platform. Your system must also be future-proof. Choose a system that will ensure long-term ROI from your investment, keep your business current and agile and costs down, improve efficiency, increase visibility, drive profitable growth, and incorporate new technologies as they become available.
Centralized and integrated modules
ERP isn’t simply a collection of software applications that have some integrated functionality. A best-of-breed manufacturing ERP solution offers a seamlessly integrated set of software modules that enable users to manage grouped tasks without switching applications or screens. Each module offers the ease-of-use of today’s best individual software components, providing all information needed for each operation in the same part of the system. At the same time, the integration of modules allows users to easily work between parts of the system without feeling like they are jumping from one software application to another.
From a user’s perspective, the overall system “feel” is that of one large application with many functional areas that freely share information in real-time. This complete integration eliminates the need for performing redundant tasks across business functions. Data entered in one function is immediately visible and accessible to others.
The benefits of centralized and integrated modules are as follows:
- Automates and streamlines processes
- Standardizes business operations
- Provides transparency and insights for informed decision-making
- Allows full, informed, and efficient production control
- Provides continually updated, real-time, accurate data
- Makes cost-efficient, just-in-time inventory possible
- Corrects production bottlenecks and business inefficiencies
- Enables the highest standards in quality control
- Improves on-time deliveries
Signs of an obsolete ERP
There are plenty of outdated ERP systems still available in the marketplace. These can have a variety of problems including incomplete solutions, time-consuming manual processes, system glitches, difficulty leveraging data, poor integration, and redundant work for your team. The three types of obsolete ERP are:
- Homegrown: Assembled, often piecemeal, with off-the-shelf tools and no roadmap
- Cosmetic: New architecture layered on top of legacy code
- Mash-up: Merging of software companies and solutions
ERP database
A central database is at the epicenter of the ERP infrastructure; it is the source from which all modules or applications retrieve information, and through which they all communicate. The central database ensures that all users within an organization are working with the same up-to-the-minute data. This eliminates the need for verification by phone or email between employees or employees and business partners or vendors. It puts an end to business inefficiency and disruption; the ERP itself is a constant conduit of reliable information.
Cloud-based architecture
Cloud-based ERP architecture provides several critical benefits for small and medium sized manufacturers and job shops:
- Economies of scale provide enterprise-grade compliance, security, back up, and support, scaled to the budgets of SMBs.
- The remote infrastructure, supported by the vendor’s IT staff, reduces IT costs and overall operational expenses for greater cash flow.
- Executives and key personnel have anytime, anywhere access to the system, and can work in the office, from home, or on the road.
- Decision-makers can track material, job status, and operator and machine availability from a laptop, tablet, or even a smartphone, without being tied to the office or shop floor.
- Employees have visibility into the jobs they’re working on, wherever they are working.
- Updates are communicated to all personnel, including machine downtime or work center changes.
- System and data is always up-to-the-minute, with an accurate reflection of your operations, financials, and inventory.
- Current data enables meaningful real-time reporting and dashboard monitoring of KPIs.
Specialized ERP functionality requirements
While your business shares much in common with competitors, you are likely quite distinct from any other players in your market. You need a system that can be cost-effectively customized through modules and add on functionality to support your needs. You also don’t want to overpay for a completely customized system that doesn’t incorporate best processes and practices for manufacturing SMBs.
Among the most essential specialized functional requirements are the following modules or features:
Visual scheduling
This functionality enables you to implement a priority system that optimizes what is worked on and when, reduces WIP by managing when material gets sent to the job floor, and ensures the right amount of each product from raw materials to subassemblies to finished products.
Full quote-to-cash core solution
This functionality automates configuring price quotes, contract management, and revenue management, while avoiding the data entry redundancy that costs SMBs so much valuable time
Production control and shop floor management
With this functionality integrated into your solution, you can easily share job information with your shop floor team, enabling you to monitor progress in real-time and manage production more efficiently. Dashboards and reporting capabilities provide business insights into production capacity, inventory, and equipment downtime. This functionality should also enable you to track labor and resource consumption, compare estimate-to-actual costs of jobs, and analyze and improve profitability per customer.
Native finance/accounting
This functionality integrates finances including accounts payable, accounts receivable, payroll, fixed assets register, and credit card processing into one secure system. The general ledger enables you to manage and report financial activities and capture and post transactions everywhere from production to shipping.
Inventory and employee time management
For SMBs, two of the costs that can be brought under control most efficiently with ERP are labor and inventory. Because this functionality integrates with all business data, you can much more easily optimize inventory levels and staffing levels to meet market demands while minimizing tied-up capital.
Hallmarks of truly advanced ERP solutions
- Optimum speed and performance including fast-loading screens, fewer clicks per task, and a system that rarely stalls or freezes
- Frequent and automatic software application updates that incorporate feedback from industry users at all levels of their organizations
- Adaptability for mobile solutions, IoT, machine learning, predictive analytics, and other new and emerging technologies
Ecosystem of value-add partnerships
Another reason for choosing a manufacturing-specific ERP solution is the many partnerships that longtime ERP providers have with myriad vendors in the industry, many of which can immediately add cost-efficiencies to your business. Talk with the providers in your consideration set about their ecosystem of partnerships.
Quality management solutions
This functionality in best-of-breed manufacturing specific ERP solutions enables you to automate and customize your requirements for inspection, analyze quality data and trends, and review improvements. You can also custom-configure these features for your quality compliance needs.
CRM
Customer relationship management empowers your sales and marketing teams to grow your business through understanding and using sales and marketing data. A CRM module provides immediate access to real-time data and tools to support more profitable marketing campaigns, as well as departmental integration, communication, and traceability. CRM tools lead to other improved customer metrics such as on-time deliveries and satisfaction with customer service.
Integrated product configurator
Today’s customers are more demanding than ever, and this functionality lets you configure products to their exact needs. You can design anything from a single-level bill of materials to complex multilevel products. You can also create and configure complex dimensional parts from quoting, order entry, job entry, and lead entry functions, if available.
An ERP solution is only as advanced as the provider
Once you have determined all the core and specialized functionality you want in your ERP solution, you can eliminate the providers that don’t offer adequate systems for your needs. At this point, you may still have a few contenders, and that’s good, because the next step is likely the most important, and will bring you close to a final decision.
From your contending providers, select one that meets the following criteria:
- Experts who want to communicate and understand your business objectives.
- Experience in complex business process problems.
- Decades of combined experience in manufacturing processes and business requirements.
- A deliberate discovery process that informs how you think about your business and technology priorities.
- Expertise in the specific challenges of manufacturing and job shop SMBs.
- A willingness to share industry trends and competitive landscape information to support your business priorities, past the point of sale.
- A fascination with process improvements to be expected from the next-generation of digital initiatives that your ERP is built to support.
An ERP Buyer's Guide for Manufacturers
- PART 1: How to Prevent 5 ERP Selection Mistakes
- PART 2: How to Champion a New Manufacturing ERP
- PART 3: How to Determine ERP Functionality Needs
- PART 4: Manufacturing Discovery Call Success
- PART 5: Plan and Build Your ERP Budget
- PART 6: How to Build an ERP Project Plan and Timeline
- PART 7: Own Your Implementation Success
Ready to Transform Your Manufacturing Process?
Take the first step towards operational efficiency and business growth. Fill out this form to get in touch with our ERP experts who can guide you through the selection and implementation process of our ERP software for manufacturers.