ERP Buyer's Guide Part 7
Own Your Implementation Success
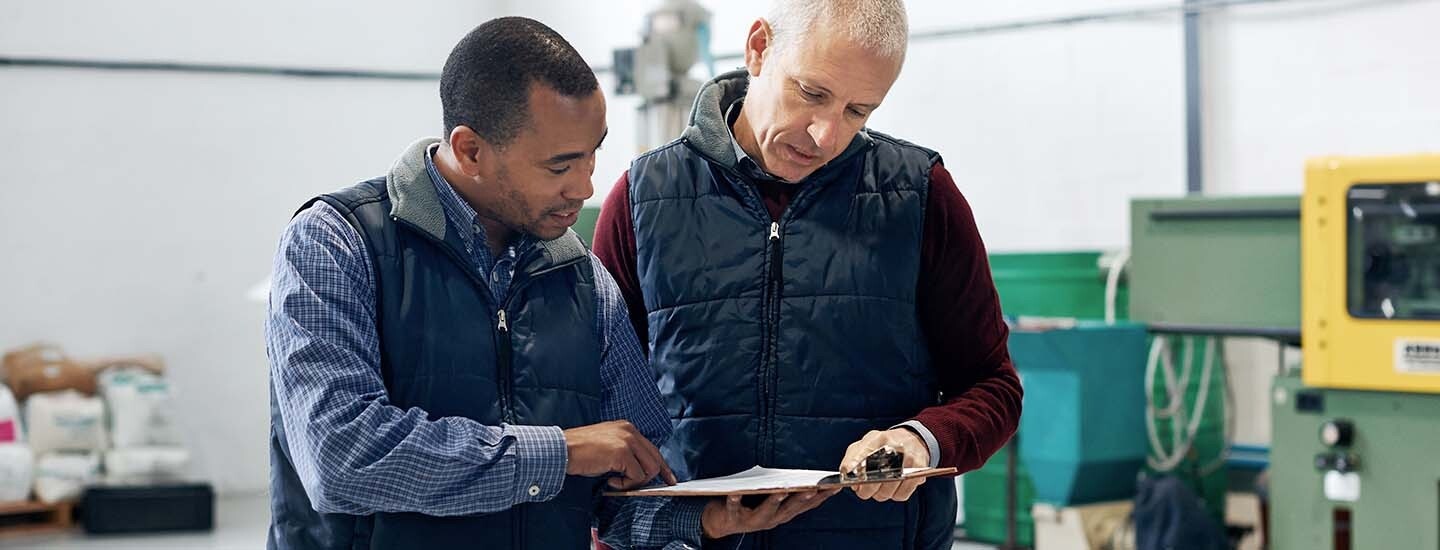
Best practices for ERP implementation
One of the best ways to gain efficiency needed to compete during a contracted market is through the use of an enterprise resource planning (ERP) software. While a best-of-breed system is essential to a manufacturer or job shop’s ability to compete, regardless of size, market, or economic conditions, the work doesn’t stop with the purchase.
There is a lot of room for error in a process that begins with defining business objectives, continues through the due diligence of auditioning vendors and software solutions, and culminates in a multifaceted implementation. The process of transitioning to a new solution is too complex and important to embark upon without first setting expectations and goals, and understanding the ways in which they can be jeopardized. By understanding why ERP implementations can fail, you can set your organization up for long-term success.
Here are 7 critical implementation best practices that, if not addressed, can complicate, delay or even scrap an ERP implementation:
- Maintain consistent executive support
- Embrace change management
- Plan accordingly with an achievable schedule
- Appoint an internal champion and support team
- Don’t skimp on training
- Ensure data quality
- Choose the right vendor/ERP provider
The following guide outlines common oversights, miscalculations, and lapses in understanding that can occur during a typical implementation and how, with the proper tools and team, you’ll be up and running in no time.
The top 5 factors contributing most to ROI for manufacturers after an ERP implementation are:
Increased production capacity without added headcount or capital investment
Reduced IT costs
Reduced cycle time
Reduced headcount dedicated to manual data entry
Reduced inventory levels
Maintain consistent executive support
Moving to an ERP requires more than a signature on a contract. To successfully implement an ERP and promote its adoption, senior leaders need to become evangelists and embrace the change. Executive buy-in is essential to getting an ERP project off the ground, but their support is necessary on an ongoing basis. They should support the project by helping set the overall goals of the project and align these with business objectives.
Embrace change management
Often, the biggest challenges with introducing a new solution like an ERP is your team and their unwillingness to change. The worst thing someone can say when it comes to implementing an ERP is “this is the way we’ve always done things.”
Your team may be comfortable managing inventory using a pen and paper instead of a computer, but the key to change management is showing them the value. What’s in it for them? Give them the training and resources they need to get comfortable with the software and actively involve them in the project. Let them help define new processes based on their subject matter expertise. Ensuring your team is set up for success and feels part of the solution will help with change management.
Plan accordingly with an achievable schedule
Think of the implementation process as a journey and with the help of the vendor’s implementation team and your internal stakeholders, map out your plan. Consider the daily action items, and the data and workflows necessary to support these steps. Be sure to audit your current system so that you can map your current tasks and workflows to the new ERP. Plot your key expected milestones including training dates for each user group, data migration and integration, go-live, and beyond.
Your schedule should be achievable and realistic, yet aggressive enough to maintain momentum through the process and minimize loss of productivity. Be careful; being too aggressive in your target dates can stress your key players and distract them from their daily responsibilities. Every company is unique, which is why some implementations go “big bang” with all departments going live at once, while others approach the process more incrementally. The schedule must be based on your available personnel and resources, their capabilities, availability, and willingness to meet expectations.
Manufacturers often underestimate the time and resources required in an ERP implementation. A good starting point to estimate your time frame is to divide the cost of the software by 100. A $25,000 investment will take about 250 man-hours to complete before factoring in the variables that will either shorten or extend the timeline.
Appoint an internal champion and support team
Many manufacturers make the mistake of thinking of the vendor-appointed project manager as the sole leader in the transition. There is a strong correlation between making the right internal appointments and achieving a successful ERP implementation.
Choose a leader with proven capabilities in managing software systems to be your internal ERP champion. This will be the project manager responsible for collecting all of the end user business requirements. They will assign training resources to different departments, groups, and individuals; work with the vendor on data migration and conversion; share information through a project management application; and be the point of contact for everyone in your organization to assure buy-in at all levels. Given the importance of this role, it is advisable to assign someone with a lengthy company tenure, influence within the organization, and excellent communication skills.
The champion should be supported by a cross-functional team, from skilled IT personnel to daily ERP users that can help to manage the daily tasks in each of the above-described areas. He or she can assign their roles and re-assign them as necessary. By delegating responsibilities, the champion will have the time to conduct frequent progress briefings of company executives and won’t get bogged down in the granular details of managing the process.
Don’t skimp on training
Change management is essential in any business transformation and ERP implementations are no exception. One of the ways in which change is mismanaged often in this process is lack of staff preparation. This is the point at which the “people factor” must be made a top priority. Wanting to keep their “go-live” dates, companies often shorten the time frame for training which is one of the most common reasons ERP implementations fail.
Work with the vendor implementation team and make sure your ERP champion communicates training timelines, what will be taught and to whom, and the resources that will be used. These should include visiting presenters, videos, and online guides. Use vendor-supplied or collaboratively designed tests to be sure that your employees have reached the expected levels of proficiency before going live.
And, don’t assume that cloud-based software or software as a service (SaaS) doesn’t require organizational change management. Just because these systems are more easily and affordably configured, and can be quickly adapted to changes in your business, doesn’t mean that they won’t change your business processes and require adequate ramp-up time for training.
The top 4 reasons for a lack of ERP implementation success are:
Inadequate quality of testing
Inadequate training
Inadequate planning/lack of readiness assessment
Inadequate business process re-engineering
Ensure data quality
Poorly compiled, poorly stored, or unclean and inaccurate data can put the brakes on an implementation and cause major delays. As a manufacturer, you can mitigate much of the risks associated with this type of problem by making sure that you have consistent, accurate, and properly entered data.
The vendor you choose to work with is especially important if you have an antiquated legacy system with inconsistencies in data that need to be accounted for or worked around. An experienced vendor will have superior methods for testing the data quality and integration with all of your new ERP applications. The scenario to avoid is that you don’t recognize any data transfer issues until they have impacted your business —and worse—that you don’t have a vendor that can effectively and quickly resolve these issues if they do arise.
Choose the right vendor/ ERP provider
ERP is an investment—if you don’t choose wisely, you can get stuck in a long-term contract with a vendor who doesn’t provide the support, training or future innovation you need. Ultimately, this will impact your day-to-day operations and how you do business.
Extensive research and planning are critical when selecting an ERP provider. You don’t just need a vendor who offers all the must-have features you’re looking for; you need a partner who will provide the guidance, support, and leadership you need to be successful. When researching vendors, be sure to ask about training, documentation, their implementation process, ongoing support, and ensure they are aligned on your business goals to help you get the most out of your solution.
The top 3 benefits of a new ERP solution:
Reduced process times
Increased collaboration
Centralized enterprise-wide data
Final thoughts on a successful ERP implementation
Your implementation leader and team is only as strong as the partnership they form with the resources your vendor offers. When implementing an ECI software, you receive a dedicated implementation guidance representative that will be an extension of your business throughout the implementation process. They check in with you to shepherd you through the process and even better are available for you to reach out to if you have any questions or need additional support. And ECI’s commitment doesn’t stop once you go live. Every new customer has a dedicated Customer Success Manager that will continue to manage your ongoing implementation and partnership for growth for life of your product.
An ERP Buyer's Guide for Manufacturers
- PART 1: How to Prevent 5 ERP Selection Mistakes
- PART 2: How to Champion a New Manufacturing ERP
- PART 3: How to Determine ERP Functionality Needs
- PART 4: Manufacturing Discovery Call Success
- PART 5: Plan and Build Your ERP Budget
- PART 6: How to Build an ERP Project Plan and Timeline
- PART 7: Own Your Implementation Success
Ready to Transform Your Manufacturing Process?
Take the first step towards operational efficiency and business growth. Fill out this form to get in touch with our ERP experts who can guide you through the selection and implementation process of our ERP software for manufacturers.