Deacom ERP Software for Batch and Process Manufacturers
Deacom is a comprehensive manufacturing ERP solution with a wide range of capabilities designed to meet the needs of small- to medium-sized businesses. This includes companies within Food & Beverage, Chemical, Health & Beauty, and Pharma & Life Sciences industries.
Manufacturing ERP that meets your needs
Unlike fragmented software solutions, Deacom consolidates all the essential functionality you need into a single system, simplifying your operations and maximizing efficiency.
Deacom Essentials Now Available!
We are now offering two packages depending on the size of your business and budget: Deacom Essentials and Deacom Enterprise. Deacom Essentials is a new offering for those smaller batch and process manufacturers who want an ERP system that they can truly grow with. We are committed to servicing businesses of all sizes and in a variety of industries.
Enable total process control
Deacom streamlines production management with built-in quality control (QC) checkpoints. This level of process control ensures compliance with customer requirements and integrates formulation management, production scheduling, and order management in a single ERP for manufacturing with centralized visibility of the entire process.
Automate processes to eliminate manual errors
Deacom ERP uses a single set of business logic for centralized data, enabling automated and accurate reporting and document generation. This eliminates the costly risks associated with manual intervention like process delays, incorrect data entries, misplaced documents, and tribal knowledge.
Reduce the cost of being wrong
Hyper-Tight Process Control™ is a unique component of the manufacturing ERP that reduces the cost of being wrong. By ensuring that specifications and compliance standards are met consistently, Deacom customers avoid the negative implications of legal claims, recalls, low customer satisfaction, removal from preferred supplier lists, and much more.
Significantly reduce inventory variances
The ERP software provides the visibility and tools necessary to fine-tune material purchases to match current production needs, sales forecasts, and production schedules. This level of visibility and accuracy is possible because all data resides in a single location.
Leverage native tools to manage complexity
- QC / CoA / Customer-Specific Requirements
- Lot Tracking / Recall Reporting
- Batch Record Enforcement
- EDI Trading Partner Compliance
- Regulatory Requirements (FDA, GHS, SQF, etc.)
- Job Costing
- Shelf-Life Adherence
- Supply Chain Management / Material Resource Planning
See how customers have improved their operations with Deacom
Deacom Customer Story: TruFood Manufacturing
TruFood Manufacturing has been successfully running on Deacom ERP for years, so when they acquired Simply Natural, they knew that using Deacom ERP for both companies would create more efficiencies and drive growth. With the foundation and SOPs already in place, along with the industry expertise of the Deacom implementation team, Simply Natural was able to get up and running in just four months.
Deacom Customer Story: Nature’s One
Nature's One needed a complete ERP solution that eliminated the long paper trail and lack of visibility that its legacy system created. With a pledge for purity in contents, quality, sourcing, and testing, the company wanted a solution that could keep up with its mission and purpose, as well as regulatory requirements. All of this needed to be done without being bogged down by bolt-on ERP customizations.
Supported Industries
Frequently asked questions about Deacom
Can the ERP system help us manage our sales forecasts?
Yes. Deacom can help you predict sales based on historical data so you can more accurately project trends in your business. These forecasts can be used throughout the system but are very useful in MRP. Within the software, you can:
- Drive the purchase of long-lead-time raw materials based on sales forecasts
- Create forecasts for products based on historical sales
- Apply percentage-based changes to the forecast based on projected trends in the business
- Import customer-specific forecasts from Excel to ensure you have the production capacity to handle expected orders
What are the production capabilities of the ERP software?
Production is at the very core of most batch and process manufacturers. Deacom’s production capabilities include planning, scheduling, inputting, closing, and reporting on production jobs.
How does Deacom help us calculate our material planning requirements?
One of the most important tools from a production planning perspective is the MRP (Material Requirements Planning) tool. Core MRP functions within Deacom help businesses:
- Reduce waste by maintaining the lowest possible material and product levels
- Gain full visibility on customer demand and supply of their inventory
- Optimize their supply chain management
- Plan manufacturing activities
- Manage delivery schedules
How do I track how materials are issued to jobs?
As part of the manufacturing process, it is critical to identify the precise lots that go into production from a raw material standpoint, as well as to document the finishes of a product with real-time visibility. Most of our customers perform these processes using scan guns and the Deacom Warehouse Management System (WMS).
Can Deacom handle my customer’s specific quality control specifications?
Yes. Deacom provides an efficient way of making sure the correct products get to your customers, especially for those that require specific quality control specifications. You can manage QC specs including specific tests, target values, and min/max values of acceptance for the finished product directly from within the software. This helps your warehouse pickers confidently identify which lots will meet those customer requirements.
Can Deacom help me with my lot tracking and traceability needs?
Yes. Deacom allows you to drill down into inventory reporting starting from the raw materials all the way to the finished goods and view the specifics of everywhere that a lot was used. Because the system is built upon a single database, full traceability is available throughout the entire formulation to shipment process.
What BI reporting is available to me?
The ability to generate reports quickly and efficiently is a significant benefit of using the Deacom ERP system. The built-in reporting tools are user-friendly, simple to set up and configure, and consistent throughout the software.
My manufacturing company has a need for environmental reporting. How can Deacom help me with that?
The Environmental Reporting feature in Deacom supports reporting requirements for emissions during production and hazardous contents of products shipped to customers. Included is the ability to run reports, generate GHS & SDS labels, and create regulatory-compliant BOMs.
We operate within an FDA-regulated industry. How can Deacom help us manage any potential recall reporting?
The effectiveness of recall management hinges on seamless traceability within your supply chain management. To support this need and conform to the FDA’s identification and traceability regulations for food manufacturers, Deacom’s ERP solution provides lot tracking, asset tracking, and serialization capabilities. This allows users to identify and trace material at each stage of the product lifecycle.
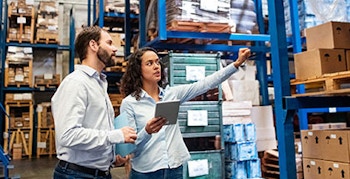
Deacom ERP Features And Functionality
Deacom provides a rich set of capabilities and extensibility designed for growing manufacturing and distribution businesses.
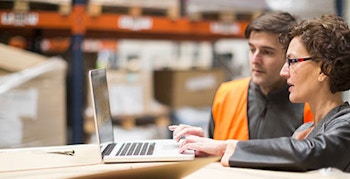
Enterprise Resource Planning For Supply Chain Resilience
The global COVID-19 pandemic, with its disruptive effects on manufacturers’ supply chains, has been a wake-up call for many…
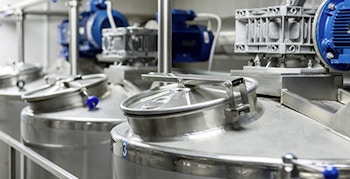
ERP for Process Manufacturers and Distributors
By focusing specifically on the process manufacturing industry and providing the capabilities to ensure Hyper Tight Process…
Hear from more of Deacom's customers
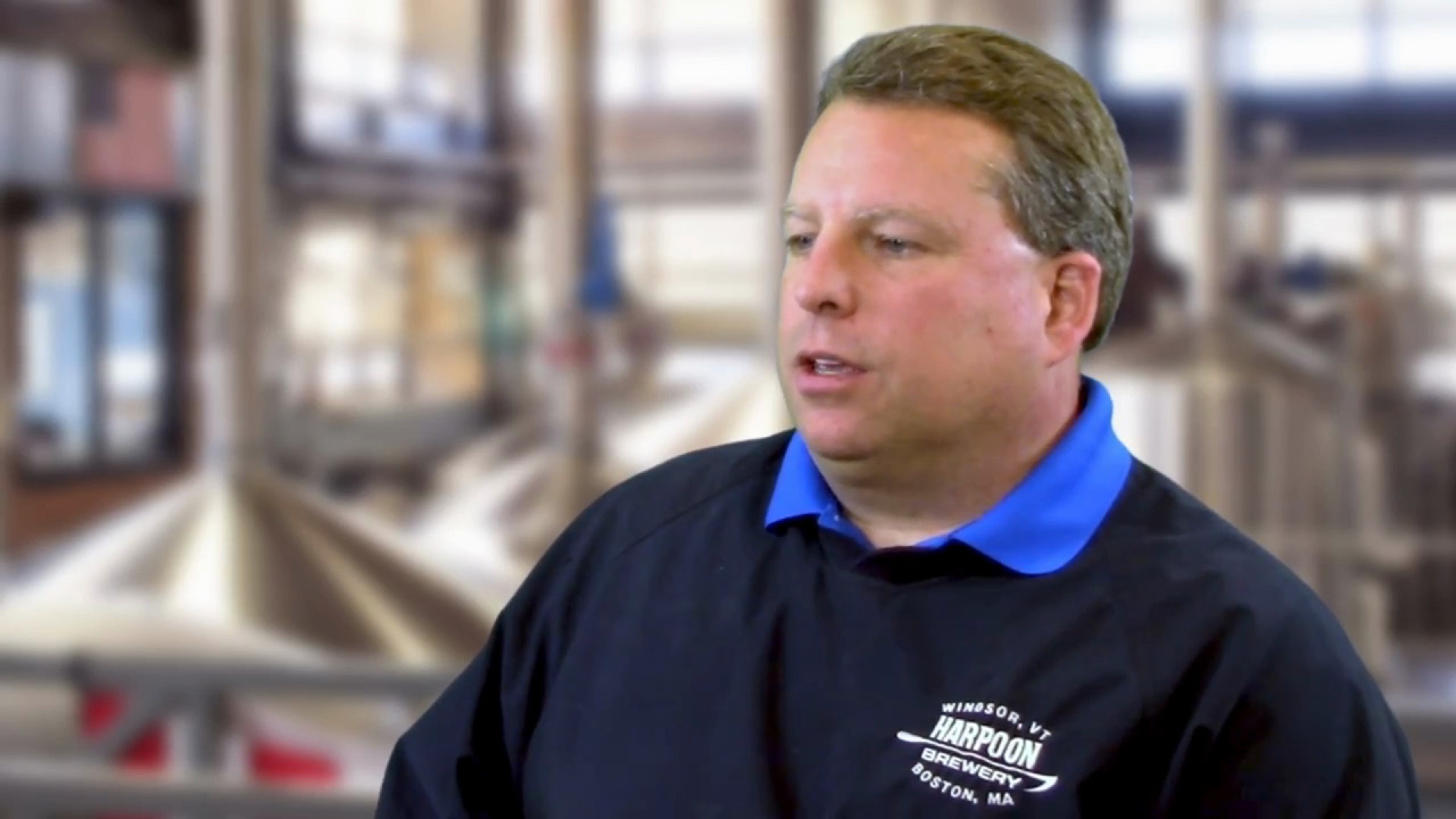
See how Harpoon Brewery gained production efficiencies by using MRP to schedule all of their brewing and packaging.
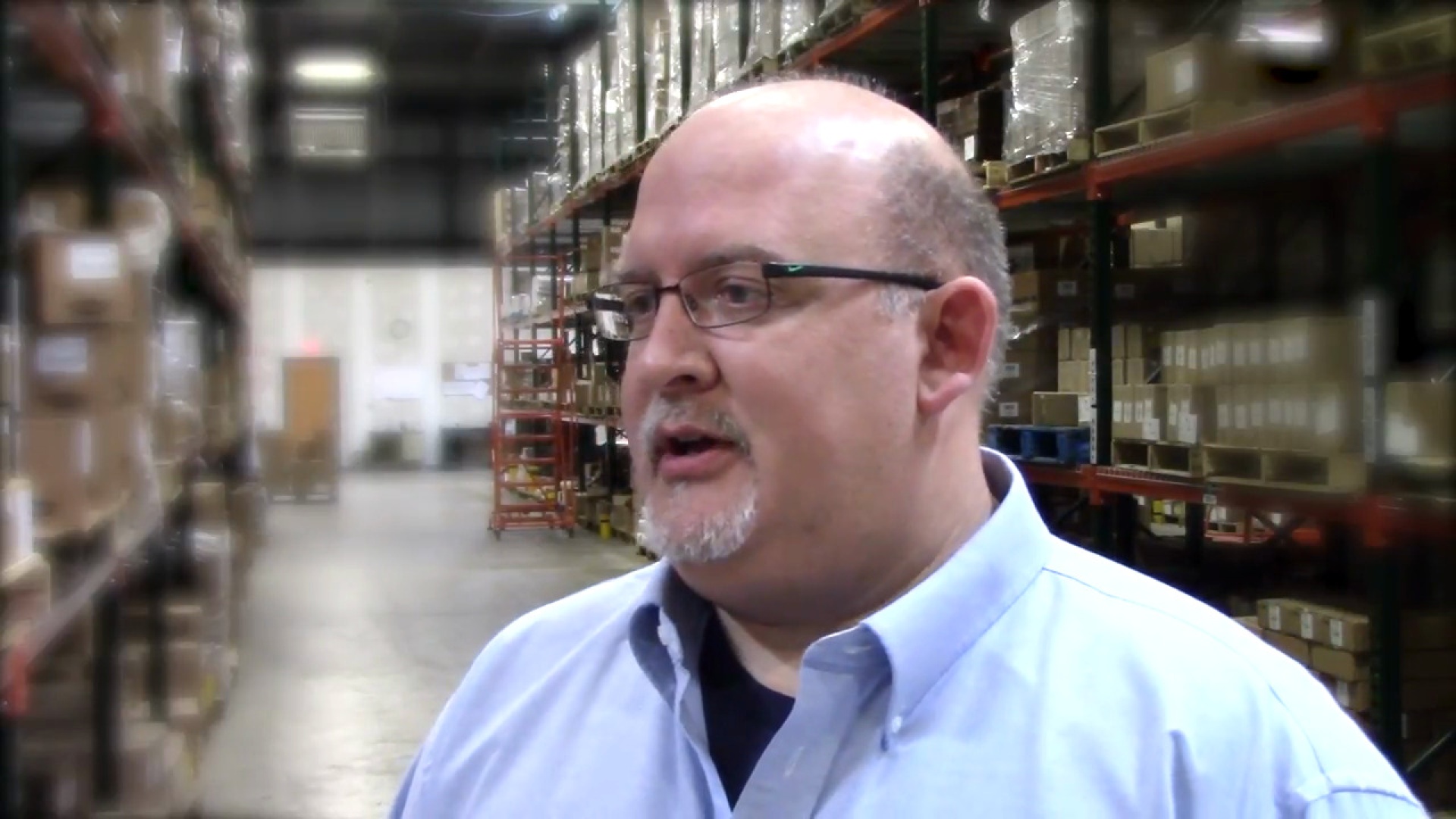
Learn about the reduction in inventory variance that Silver Spring Foods achieved after implementing Deacom’s WMS system.
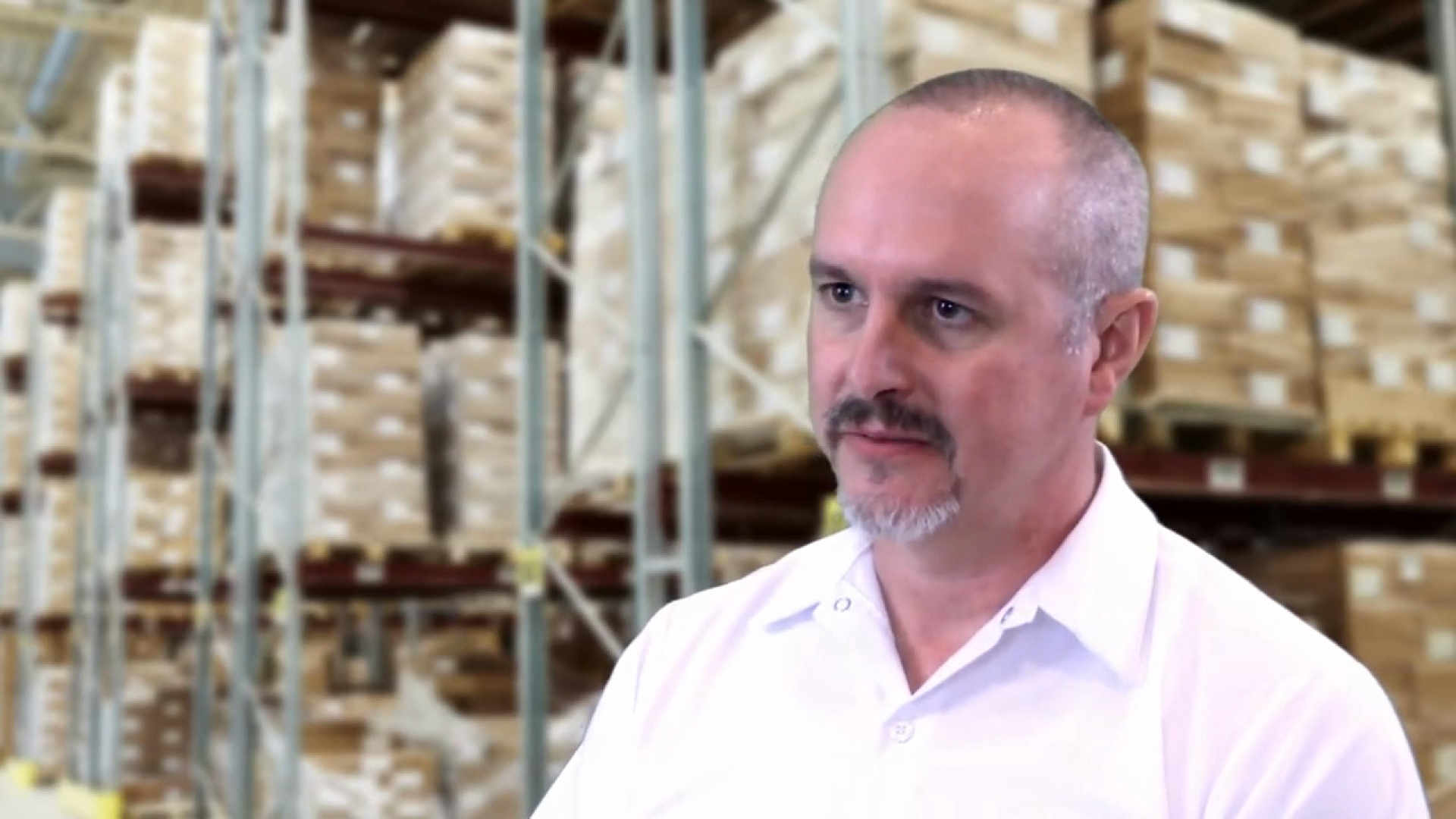
Hear how Graceland Fruit’s use of Deacom to track inventory control forward and backward provides them with full traceability – down to the individual tote.
Are you ready to uncover the possibilities with a comprehensive ERP?
Reach out to us now and see how Deacom ERP can transform your manufacturing business.