Reduce the "Cost of Being Wrong"
Hyper-Tight Process Control™ in Process Manufacturing
It only takes one mistake – one distraction, contaminant, or error – to make a dramatic impact on your business. You never want to be the subject of a recall headline, turn away business because production had to be unexpectedly shut down, or threaten the health of consumers. But the fact is, that one mistake has the potential to destroy your reputation, your sales, and ultimately your bottom line.
The competitive marketplace and historic decline in customer loyalty raise the stakes for businesses that have a high dependency on each and every customer. The expenses associated with trying to fix that one mistake and regain the ground that has been lost can be significant. This is what we call: the “cost of being wrong.”
Batch and process manufacturers, in particular, cannot afford to be wrong in this market. With the right processes in place, the “cost of being wrong” can be minimized. Hyper-Tight Process Control™ allows businesses to enforce scalable and repeatable processes that cannot be bypassed by employees. It provides businesses with improved visibility and control with quality checkpoints that ensure that specifications and compliance standards are met consistently – even if the entire process must come to a halt during the journey. It enables companies like yours to identify quality issues within the supply chain as soon as possible and fix or eliminate them before they become problems downstream.
Hyper-Tight Process Control™ is what empowers companies to circumvent unnecessary mistakes and maintain the level of quality that customers have come to expect. This white paper is focused on complex processes and how businesses that rely on Hyper-Tight Process Control™ can avoid the “cost of being wrong.”

The "Cost of Being Wrong"
Imagine you produce yogurt for a big wholesaler. Upon receiving the product last week, the wholesaler conducted their own Quality Control (QC) testing and discovered that your yogurt was contaminated with a pathogen, so they asked you to take the yogurt back – now you
have lost revenue. Today, the wholesaler shared that they have lost trust in your ability to deliver quality products, so they are not going to order from you again. Instead, they will give their business to a competing brand. Now, in the blink of an eye, you have lost your preferred vendor position as well.
A single mistake like this can come at an unquantifiable cost. In recent years, there have been many recalls as a result of avoidable errors. In 2020, Whole Foods Market recalled more than 30 food products that had undeclared food allergens1. Whether products were mislabeled, or incorrect materials were added to a production batch, these mistakes risk the health and lives of millions of families who have food hypersensitivities.
For manufacturers in regulated industries, the “cost of being wrong” can add up to billions of dollars in fines, wasted products, lost or reduced sales, and a tarnished reputation that may never recover. The good news is that these costs are avoidable.
Businesses can start – and protect against future mistakes – by ensuring that processes are controlled, that quality issues are detected as early as possible and, if an issue occurs, processes are stopped immediately with no way to bypass them. Having this level of tight process control can help organizations reduce the “cost of being wrong.”
Process Control - A "Must-Have" for Process Manufacturers
Turning raw material into a finished product can be complex. Most discrete manufacturing that requires only a few steps, such as furniture production, is fairly straightforward. Yet process manufacturing is often much more complex, involving many intermediate products and hundreds of steps to make a single finished good.
Hyper-Tight Process Control™ Advances Traditional Process Control
Process control is most often used in continuous production where products are being produced without interruption. When used correctly, it can help ensure a consistently high level of quality and efficiency.
In order to achieve process control, traditional ERP environments will often bolt-on software to deliver production planning and execution, receiving, shipping, document generation, quality control (QC), and manufacturing execution systems (MES) systems. This form of process control requires heavy integration of systems and data in order to connect all solutions components and provide a transparent view of what’s going on in production. It also introduces weak points into the process by creating gaps in the flow. When any component is not supported by the integration, data must be manually entered and maintained in separate applications like Microsoft Excel, Access, or any other database. This leaves that branch unmanned and unmonitored.
Hyper-Tight Process Control™ takes traditional process control to the next level by providing a holistic approach, eliminating the risk factors. It mandates that supply chain planning, manufacturing operations, and quality control (QC) functions are native parts of the core ERP system. This emphasizes full control of processes, from receiving to shipping and document generating, and is coherent enough to stop the process at any point in time. Since Hyper-Tight Process Control™ draws from the same system that controls manufacturing operations, supply chain management, quality control, and warehouse management, it is able to control any of the processes initiated by these systems.
Hyper-Tight Process Control™ is designed to protect against human error by putting in place fail-safes. Each fail-safe stops events where team members may violate or ignore alerts, and issues documentation at each stage of the process. With feedback loops built right into their ERP software environment, batch and process manufacturers can confidently assure their customers that they will do what they say they will do.
Organizations that use Hyper-Tight Process Control™ can:
- Interweave manufacturing processes with quality checkpoints across the whole product lifecycle, from receiving raw material or intermediate products through issuing to production, finishing products, and shipping to the customer.
- Prevent the bypassing of quality checkpoints.
- Avoid mistakes caused by human intervention from interfering with high-quality finished goods.
- Manage warehouse, production, process, and quality control from one ERP system.
With Hyper-Tight Process Control™ from within Deacom you establish a tight process control and -
- Reduce the “cost of being wrong,” which includes potential legal claims, recalls, reduced customer satisfaction, deletion from preferred supplier lists, etc., by:
- Detecting quality issues as soon as possible, preventing error-based cost explosion.
- Securing and delivering quality independently of production/business load or specific people.
- Gain process visibility and data accuracy with real-time information due to its interoperability with all other ERP functions involved in the supply chain, production, shipment, document generation, and quality management process.
Eliminating Miss-Shipments with Hyper-Tight Process Control™
Bergin Fruit and Nut uses Deacom ERP with native WMS to ensure they consistently adhere to rigorous quality control standards as their customer demands shift. With Hyper Tight Process Control™, the food manufacturer has been able to ensure that critical process steps are always followed.
Hyper-Tight Process Control™ - Why Should I Care?
Hyper-Tight Process Control™ enables companies like yours to create scalable and repeatable business practices with no breaks in process control. Imagine if, when goods are received, the quality of some batches is not checked according to customer specifications. The wrong
components or ingredients may have been used, or there may be too many components or too few of them. If left unchecked, these errors could carry over to the finished item, introducing a number of potential problems with intermediate or finished products. The sooner such quality issues can be identified in your supply chain, the easier it will be to fix or eliminate the problem, thus reducing the overall economic burden associated with these unfortunate mistakes.
Hyper-Tight Process Control™ is the key to avoiding risks like this as well as the potential for legal claims, recalls, reduced customer satisfaction, and other pressures that could damage your business at any moment. The “cost of being wrong” can range from a few thousand to billions of dollars, not to mention the tarnished reputation, unless you have successfully implemented Hyper-Tight Process Control™ in your business.
Cost of Being Wrong: The 1-10-100 Rule
In his blog about the cost of quality and the 1-10-100 rule, consultant Michael Canic explains that prevention is less costly than correction – and correction, in turn, is less costly than failure.
- Cost of prevention – What does it take to get things right on the front end? Design good processes, teach the necessary procedures to employees, deploy the right quality control systems.
- Cost of correction – This is the cost of fixing things after a problem has been detected. Rework, discard, re-engineer, apply additional cleaning measures.
- Cost of failure – There is a resulting downstream cost when a problem goes unfixed. Dissatisfied customers may not buy the product/brand again, negative comments could influence others to not make a purchase, the brand may be permanently damaged.
To minimize your “cost of quality” and avoid the “cost of being wrong,” businesses must invest in prevention – not in quality correction or handling the aftermath of a failure. The actual process should not allow companies to slip up at all. By implementing tight process control at the earliest possible stage (ideally at goods receiving) and through production to shipment, you can minimize the “cost of being wrong” and protect your brand by securing your quality levels.
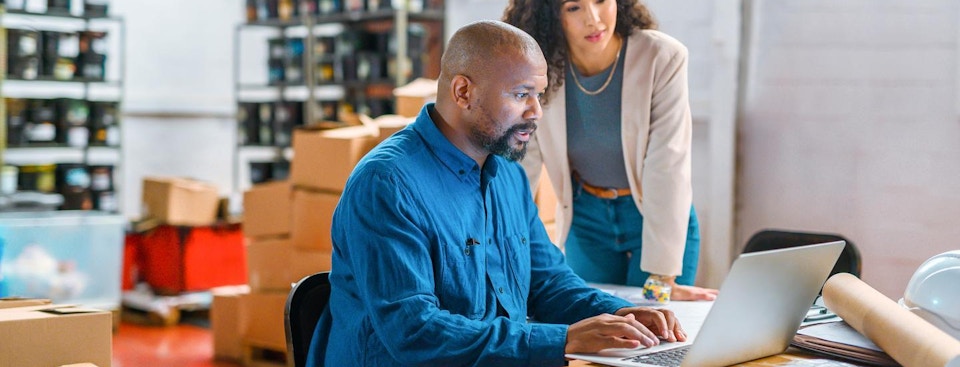
Hyper-Tight Process Control™ from One System
By visualizing and controlling the complete process of production – from formulation through shipment – in one system, organizations are able to better monitor, manage, and remediate their processes.
The central system that brings all processes together is the ERP system. This structure is what provides the high level of process control necessary to secure the execution of definable quality checks. If quality checkpoints are set correctly, Hyper-Tight Process Control™ helps to stop the whole process at the earliest point in time (preventing the 1-10-100 rule explosion of cost) when quality specifications are not met
Implementing Hyper-Tight Process Control™
- Educate your Supply Chain Management staff about the value of strong quality control and how it impacts the “cost of being wrong“ with the 1-10-100 Rule.
- Determine and document which elements of your supply chain are quality-critical (Procurement, Quality Control, Receiving, Production, Shipping, Document Generation).
- Define the process checkpoints and quality data specifications/formulas on an item/recipe/customer level.
- Define escalation procedures when a process stop is indicated.
- Make sure all affected ERP components (Procurement, Quality Control, Receiving, Production, Shipping, Document Generation) are ideally in one system and work seamlessly with each other.
- Test and refine the system.
Process Checkpoints
The chart above shows the product lifecycle from a process manufacturing perspective and potential checkpoints, including the customer and end-user process steps, for potential recalls. By enforcing process checkpoints at various points of the product lifecycle, manufacturers are able to confirm that data or calculated values from that step meet the specifications that are defined in the core ERP. Based on defined tolerances, this QC check will either allow continued progression of the process or stop it, asking for higher-level resolution of that conflicting data.
Hyper-Tight Process Control™ prevents these system-generated stops from being ignored and further steps in the process from being taken. Unless every QC check has been successfully passed, the ERP will not allow printing, shipping, and document generation, preventing those products from leaving the facility.
As companies grow and new employees are introduced to the process, the system may be challenged. But with Hyper-Tight Process Control™ interwoven within the ERP system, the built-in, multi-stage gates ensure defined processes are always followed, enforcing constant quality each step of the way.
MRP / Scheduling
At the MRP / SCHEDULING phase, the ERP system calculates what needs to be bought or produced at what time so that the necessary materials are ready for a scheduled production run. In order to properly drive MRP, data around what has sold and what is planned to be sold in the future is required, in addition to what is currently in inventory or stuck in QC quarantine.
MRP takes the formula and explodes it through the sales forecast, or sales orders, to detail what needs to be purchased or produced to fulfill a sales order – all the way down to the lowest level of materials. Having procurement, production, warehousing, and shipping in one system allows MRP to have clear real-time visibility into all materials available and ensure that Hyper-Tight Process Control™ is being upheld with QC checkpoints when necessary.
Purchase Order Receipt
The MRP step initiates the transactional flow with the PURCHASE ORDER RECEIPT process. When a purchase order arrives, the ERP system
identifies the inbound inspection of those materials to ensure that what is being received is being held before it is issued to production.
Quality Control Check
When the quality control system requires a QUALITY CONTROL CHECK for a product, the product will go into a quality control hold so quality specifications are checked. Without the proper system in place, this step is often in danger of being bypassed, especially if somebody is new to this process or the process is handled manually. This is common if production is behind schedule or there are pressures from the receiving department.
With Hyper-Tight Process Control™, the ERP system will prevent this quality control checkpoint from being bypassed. Having warehouse management and quality control functions as part of the main ERP, the system ensures that these received materials are put on QC hold until the lab has documented the results of the inspections based on specifications and, through electronic signatures, released that inventory from QC hold. Since WMS and barcoding are part of the ERP, if someone tries to scan what is on hold and issue it to production, the system will stop the operator immediately.
Issue to Production
Once the material passes the QC tests and is signed off, it is ISSUED TO PRODUCTION. This issue process is done most of the time through WMS by using scanners. With Hyper-Tight Process Control™, the WMS knows about the QC checkpoint and prevents the process from moving forward if quarantined material is attempting to be issued to production.
Finish Job
After production FINISHES the JOB, the ERP system identifies the finished good specifications and ensures that those goods are not shipped out until someone in the lab has documented the results and electronically approved them for release. The finished job process checkpoint
is another highly recommended checkpoint that is managed by Hyper-Tight Process Control™. It prevents inaccurate material from being used, reduces the 1-10-100 rule from reaching the dreaded “10-100” part, and reduces the “cost of being wrong.”
Quality Control Check
The first quality control hold was for raw materials, while this QUALITY CONTROL CHECK was for the actual finished goods. At this point, it is important to ensure that the physical properties of the finished good matches what is expected and defined in the core ERP system. If any of the previous processes have been bypassed, this quality control hold will detect it so issues can be addressed before the product is shipped out of the door.
Shipping
If employees bypass the post-production QC quarantine at the SHIPPING stage, products that may not adhere to customer or general quality standards can be shipped out. Or, maybe even the wrong product altogether may be shipped. With the Hyper-Tight Process Control™ in place, this risk is avoided and management can rest assured that their team members will always ship the right product to the right customer.
Generate Documents
GENERATING DOCUMENTS, such as bill of lading, COA, packing lists, or a pro forma invoice, can be another Hyper-Tight Process Control™ checkpoint. If the incorrect lot or one on QC hold is being picked, the ERP will prevent the operator from generating and printing the required documents for shipment. This ensures that what is done is controlled by what is defined in the company’s quality guidelines.
Customers / End Users
The last step is when the product reaches the CUSTOMER, and potentially the END USER. As you get closer to this step, the cost of being wrong increases and this is not the place to find a quality control issue. With Hyper-Tight Process Control™, you will have the controls in place to ensure you won’t.
Cost of being wrong about demand planning:
From a forecast demand to a sales order demand or safety stock associated with min/max, companies need to ensure the inventory levels they are maintaining can meet those demands. If Materials Requirements Planning (MRP) and scheduling are done outside of the main ERP system, there is a good chance that the right materials are not being purchased at the right time.
There are also cases where inventory levels are too low which can push out production runs because inventory is not available and ultimately delays shipment dates to customers. On the other hand, there may be times when a higher-than-normal level of on-hand inventory is being maintained. This can tie up cash flow, take up valuable space in the warehouse, or even make companies think they need to rent more space when it may not be necessary at all.
The Solution:
By having all the functionality associated with MRP and demand scheduling, Deacom ERP provides you with the information to make the right decisions on what to purchase and when to purchase so your inventory levels meet your demands.
Advantages of a Hyper-Tight Process Control™
Hyper-Tight Process Control™ is interwoven throughout Deacom ERP’s planning, procurement, receiving, production, quality, shipping, and document generation functionality, allowing real-time access and management of the formulation to shipment process.
With Hyper-Tight Process Control™ businesses can create scalable and repeatable business practices to deliver continuous high-quality products, eliminating the “cost of being wrong,” preventing potential legal claims, recalls, low customer satisfaction, and the deletion from preferred supplier lists.
By implementing process stops that cannot be bypassed throughout the product lifecycle, manufacturers can detect quality issues early so resolutions can be made with minimal expenses. These checkpoints also help companies grow their businesses without increasing process complexity or adding resources for quality control in order to secure full quality compliance.
Ensuring Hyper-Tight Process Control™ Requires:
One System
ERP core functionalities, procurement, warehouse, production, shipping, document generation, process, and quality control should be native to one solution. If any of these components are done in a separate system, manually, or outside of Excel, then critical steps can be easily bypassed or done incorrectly, causing breaks in process control.
Quality control procedures and measures
Quality control procedures and measures can be defined at the parts and formulation level within the core ERP.
Configurable quality checkpoints
Quality checkpoints can be placed at any stage to meet the unique needs of the business.
Prevention of Checkpoint bypasses
If quality measures are not met at process quality checkpoints, the system must stop executing the process, even if previous ones have been skipped.
Hyper-Tight Process Control™ is unique to Deacom ERP. Since all functionality – from accounting and formulation through shipping and reporting – is native to the core ERP solution, process manufacturers are able to create scalable and repeatable processes that ensure high-quality products each and every time. The software offers a unique approach to ERP that enables companies to scale their business efficiently and become a true competitor in their field of expertise.